When simulations and laboratories aid with loss adjustment
When you call on a loss adjuster, you usually expect them to come with sound technical expertise and knowledge of specific equipment or area of business. Their job is to understand and determine the cause(s) of a claim then assess and allocate liabilities. In most cases, this loss adjustment work is enough to establish the conclusions. Yet in other, more complex situations, an independent laboratory is required to bring the case to a close in a factual and objective manner. A few examples.
When is an independent laboratory commissioned?
- An industrial company can call directly on a technical investigation laboratory instead of submitting a claim to their insurer. The laboratory assists the company’s technical department in establishing the causes of damage.
- Industrial firms or individuals can also turn to their insurer after encountering a technical issue, whether there is tangible or potential damage, or a risk following a failure while testing their product.
In the event of equipment breakdown, civil liability or product recall, there will be a preliminary phase of analyses, reconstruction, or investigation of the cause(s), before studying or validating the solution to be adopted. When a case is particularly complex and requires specific technical expertise to provide the parties involved with an indisputable answer, we can turn to independent external laboratories, which may or may not be accredited by COFRAC (1) or another body. In most cases, assessment work in the INQUEST laboratory is enough to establish the conclusions.
The INQUEST laboratory can serve as an independent, objective technical guarantor in three ways, as illustrated by these examples.
Straightforward technical appraisal of a product
There was the case of a solar wall light which, according to the importer’s customers, caused fires. We can work with either the product directly involved in the incident or an identical new product provided with its technical documentation, and our conclusions may be included in the loss adjustment report.
Working with their insurer, the importer called on the INQUEST laboratory for a technical appraisal to assess the extent of the risks.
The product was a night light unit featuring a small solar panel. In daylight, the solar panel charges the battery and at night, the battery supplies the low-energy lighting.
After reproduction of the internal electronic circuit, assessment of one product involved in a fire and one new product showed that the battery management system was not compliant with minimum industry standards for the type of battery technology used (lithium).
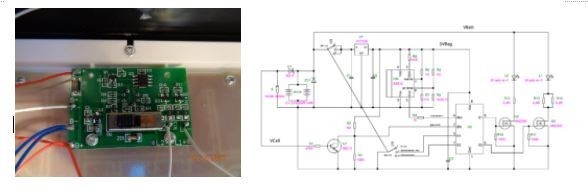
The analysis concluded that the product should be recalled.
Simulation with digital modelling or construction of a mock-up
Breakage of the overmoulding on a coil (2)in a HVA/LV power transformer (3) lead to overloading in the delivery substation of an industrial site.
The breakage observed is typical of an unforeseen mechanical constraint following statically indeterminate assembly of the overmoulding supports. The manufacturer contested this hypothesis, stating that in this case, the fracture would not have had the observed shape. To prove to them that the damage that one would logically expect to occur did indeed match the actual damage, the laboratory produced a mock-up to visualise the internal efforts endured in the material by exploiting its photoelasticity.
This is a branch of optics that draws on the birefringence (4) properties of certain materials subjected to mechanical efforts. It was frequently used in design offices, most notably in the 1930s, before digital computers came into existence, to visualise lines of force in parts subject to stress. The method is still very useful for establishing a rapid diagnosis of the distribution of efforts in a part or assembly.
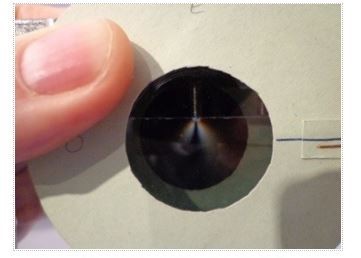
On the photograph above, through the round opening we can see the mechanical pressure on the part (bright vertical line at the top) and, below, the two lines of force in the material, due to the external bearing point, forming approximately 60° between them and their splayed section. The outcome is a vertical fracture directly below the bearing point, limited in length.
Reconstructing an incident
Following the fire of a bathroom fan heater, the insurer asked the INQUEST laboratory to examine the product in question. An initial inspection revealed that the heater did not have an anti-tipping device which would stop the heating function if the unit is tilted.
To reconstruct the incident, a new product was switched on then tipped over onto the floor littered with hair, similar to those found on the carpet in the bathroom that suffered the fire. As it fell to the floor, the fan sucked in the hair, which instantly caught fire on contact with the heating elements.
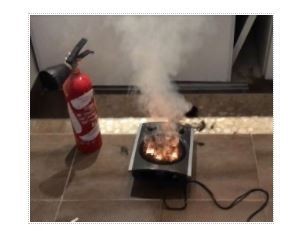
These are just three cases, three examples where the conclusions attained by the INQUEST laboratory provide a factual and objective explanation of the damage. Following the laboratory’s analysis, the loss adjustment report may recommend a product recall campaign. This would have two benefits – one for the image and reputation of the company involved, and one for consumers’ health and safety.
Pierre Monsallut
Loss adjuster and head of the INQUEST laboratory
Stelliant Group
- (1) COFRAC: COmité FRançais d’ACcréditation, the French national accreditation body
- (2) This is the insulating coating on the electrical winding in the transformer, providing electrical insulation from the exterior and mechanical support of the wires.
- (3) HTA: High Voltage A (voltage level up to 50,000 V for alternating current)
- (3) LV: Low Voltage (voltage level up to 1,000 V for alternating current)
- (4) Birefringence: Physical property of a material in which light is split in an anisotrophic manner (in different directions).